紙漿製程
Alfa Laval has a wide range of equipment and many years of process know-how and development to sustainably optimize separation processes in pulp production. Our experience also takes in heating, cooling, evaporating and condensing duties in a range of applications from wood yards, fiber lines and recovery areas to chemical islands and wastewater treatment plants.
Energy and resource efficiency in your pulp mill production
- Improved heat recovery and energy efficiency
- High chemical recovery and waste minimization
- Extraction of valuable by-products
- Increased uptime and production
- Compact design and small footprint saves on installation
Alfa Laval’s broad range of equipment includes gasketed and welded heat exchangers for heating, cooling, evaporating and condensing in various pulp and paper applications. Our high-speed separators efficiently clean lube oil and function as the heart in many tall oil systems worldwide. Decanter centrifuges help minimize waste for disposal in wastewater treatment plants and green liquor dregs handling.
Easy handling of fibrous process fluids
Alfa Laval heat exchangers are optimized to process fluids containing fibers and other solids with ease while providing high thermal efficiency and maximum heat recovery. Other benefits include low installation, operation and maintenance costs as well as complete access to the heat transfer surface to ensure easy cleaning.
Gasketed plate-and-frame heat exchangers
Our Gasketed plate heat exchangers are optimizing heat transfer by large surfaces of corrugated plates drawing heat from one gas or liquid to the other. The high efficiency and an outstanding reliability in a compact design, offers an investment with the most attractive CTO over the product life time. Not to forget the energy saving capabilities and low environmental footprint.
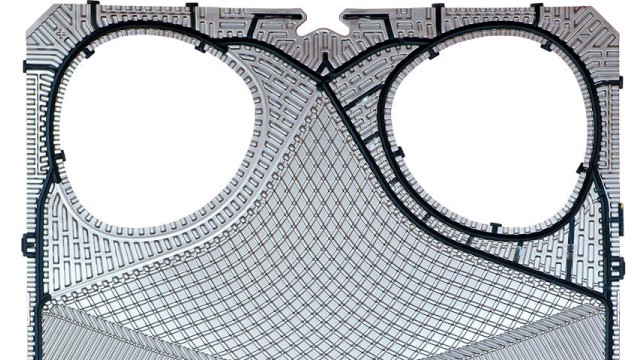
Welded spiral heat exchangers
Alfa Laval spiral heat exchangers are designed to handle the toughest heat transfer challenges. Whether it’s frequent fouling from dirty media, or limitations from pressure drop and floor space, they are the ultimate problem solver for liquid-to-liquid and two-phase duties. The robust, efficient and compact designs keep both installation and maintenance costs extremely low, and they have a proven reputation for almost never fouling up
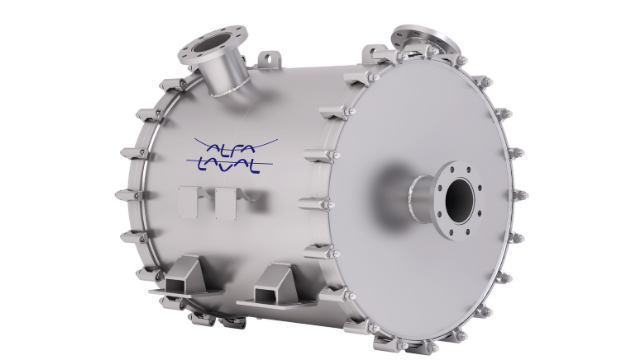
Compabloc
With over 30,000 units handling tough duties worldwide, Compabloc is the market champion when it comes to heat transfer. Laser-welded construction offers superior reliability in duties with aggressive media and high pressures and temperatures. Compabloc also offers 3-5 times the thermal efficiency of traditional shell-and-tube solutions, with a more compact design that is much easier to install and service.

How the WideGap heat exchanger works
The WideGap heat exchanger is tailor-made to handle fibrous fluids, highly viscous fluids, and fluids containing coarse particles. Because of the plate pattern and pressing depth design, these fluids flow easily through the heat exchanger.
The heat transfer area of this gasketed plate-and-frame heat exchanger consists of a series of corrugated plates, assembled between the frame and pressure plates, which retain the design pressure. The sealing between the plates is made of gaskets. For the highest thermal performance and to enable a very close temperature approach, fluids normally run counter-currently through the heat exchanger.
Soap treatment and Tall oil production
Alfa Laval has a long history in tall oil production, using centrifugal force to drastically improve yield and the highest product quality using high-speed separators. The same technology can be applied also separating the soap from black liquor. Only minutes are required to separate soap from black liquor and produce high-quality crude tall oil.
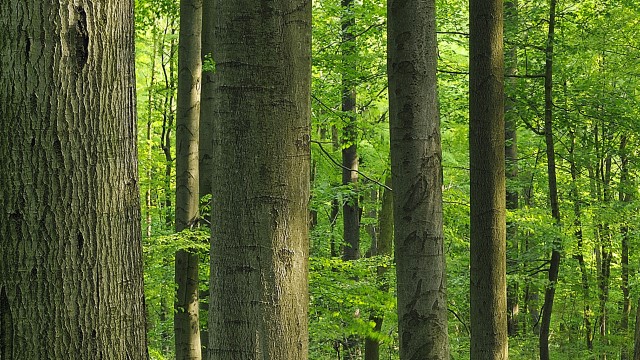
Green liquor treatment
The green liquor handling acts as the kidney of the pulp mill and removes the non-process elements, simultaneously ensuring process chemicals to be recovered and reused time and time again.
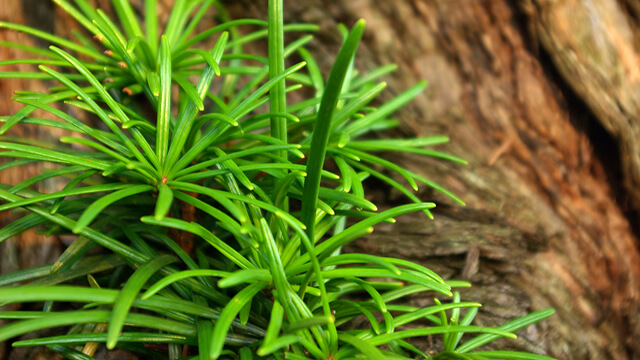
Lube Oil Cleaning
All oils contain water, to a certain degree. But when water contaminates the lube oil through leakages and condensation, and the levels rise, this can cause severe problems. For the pulp and paper industry, water is the primary cause of bearing failure.
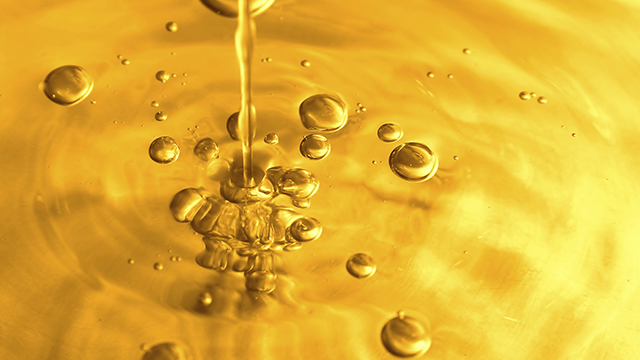
How can we help you?
Do you have questions about Alfa Laval's Heat Exchangers?
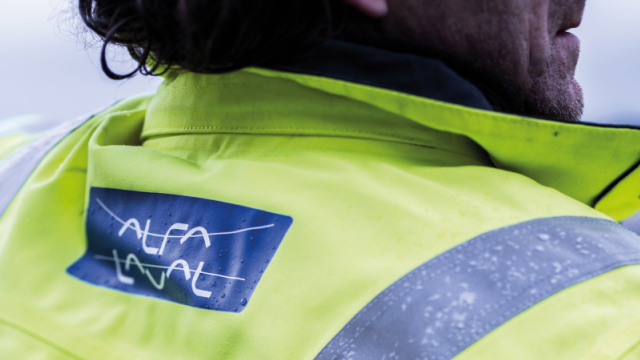
Do you have questions about Alfa Laval's Centrifugal Separators?
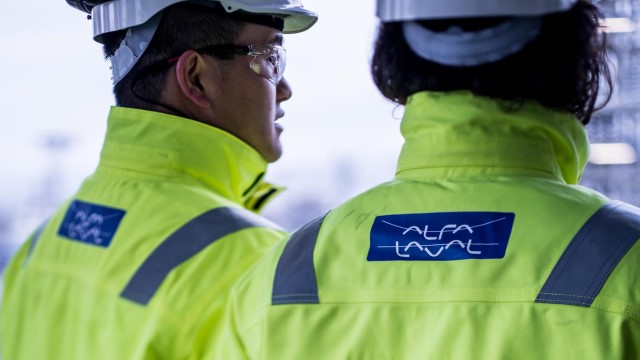