Processing plant-based liquids in dairies
Many dairy companies are expanding into the plant-based drinks sector. Some choose to invest in greenfield units with the capability to convert plant raw material into finished products. Other companies see plant-based drinks as an opportunity to utilize extra capacity in an existing dairy or beverage plant. Here the starting ingredient is either a plant-based liquid, bought in bulk, or a plant-based powder which is hydrated, i.e. mixed with water, to form a base liquid. In both cases, the base liquid is processed into the final product and packaged in the existing processing line. Our experts are here to assist you with advice on how to upgrade your plant to handle plant-based liquids. With our extensive portfolio of processing equipment, we can make sure you get an optimum solution.
Effective powder mixing
In processes where powder is the starting ingredient, one of the main challenges is getting a homogenous base liquid when mixing the powder with water. Protein fractions are especially slow to hydrate and prone to cause lumps. Effective powder dispersion is key for a well-working process and affects processing time, plant capacity, and the quality of the final product.
At Alfa Laval we have vast experience from supporting customers with solutions for preparation of beverages from recombined powder ingredients. Our powder mixers ensure instant hydration and dispersion of all powder types, including gums and protein isolates, thereby minimizing production time and ensuring great taste and texture.
New ingredients, new challenges
An important factor to consider when starting to process a plant-based liquid in an existing dairy, is that it has a different molecular composition than milk. Both the proteins and the sugars in plant-based liquids are different from those in milk, and react to heat differently.
This means heat treatment and pasteurization stages must be optimized for plant-based liquids to avoid problems. Heat exchangers that were designed for plain milk will foul much faster with plant-based formulations, with a negative impact on colour and taste of your product as a result, as well as shorter runs between cleanings.
Our service engineers can help you upgrade your existing heat exchangers to handle both milk and plant-based liquids. With a range of different plate designs to choose from, we can help you customize your heat exchangers for processing both milk and plant-based beverages, making sure fouling is kept at a minimum.
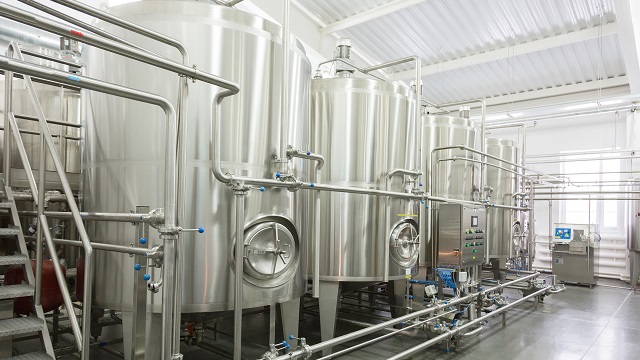
Stricter cleaning requirements
New types of ingredients also increase the demands on cleaning. Compared to processing milk, the main challenge when switching to plant-based liquids is the insoluble fibres. If you process plant raw material in your plant, you will also have to handle large amounts of particles in the upstream part of the extraction stage. We are glad to help you analyze your process from a cleaning perspective and advise you on how you can design it for minimal cleaning
We offer a range of cleaning equipment, including CIP and tank cleaning systems. Together with Alfa Laval valves and control systems, cleaning can be automated to a very high degree, which minimizes downtime and enables more efficient cleaning procedures.
We perform risk evaluations from a cleaning perspective on all parts of our equipment, especially those parts that have direct contact with the product. Based on these assessments, we make recommendations on cleaning procedures and intervals. Our CIP programs are optimized for both effectiveness and efficiency, ensuring short cleaning cycles and low consumption of water and cleaning agents.
In addition, Alfa Laval valves make it easy to create parallel systems in your plant, allowing you to operate parts of it while other parts are being cleaned. This flexibility can increase uptime and productivity greatly.
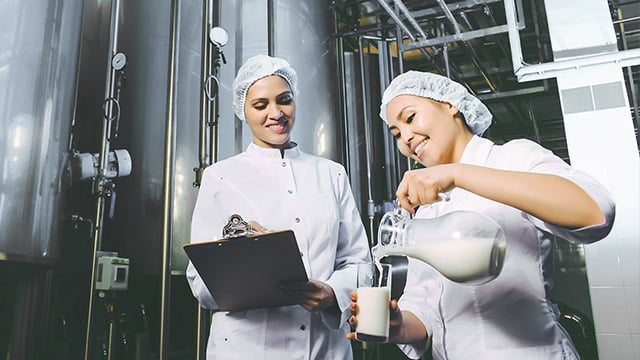